Vacuum Casting Services
Get precision vacuum casting services for high-quality prototypes and low-volume production. Our skilled team and advanced equipment ensure fast turnaround times and impeccable quality. Trust us as your vacuum casting manufacturer for reliable and cost-effective solutions.
- Quick quotes with complimentary DFM feedback
- High-quality, production-ready parts
- Once the prototype mold is ready, we can ship the product within 1-2 days.
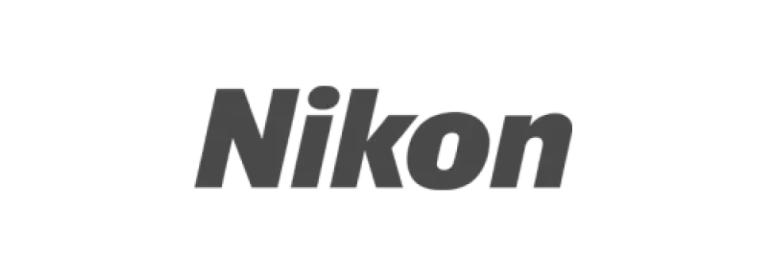
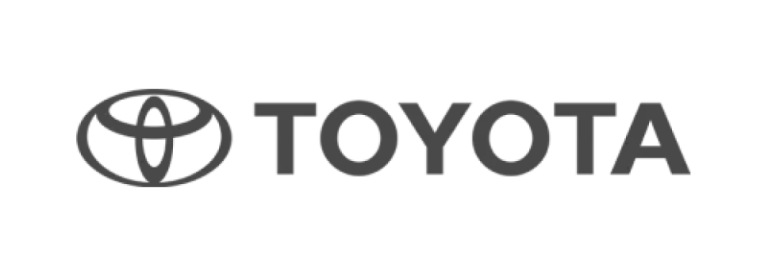
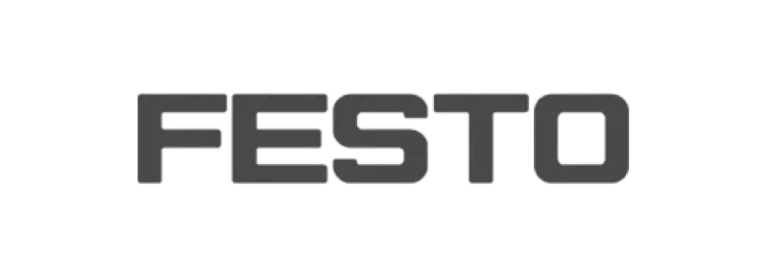
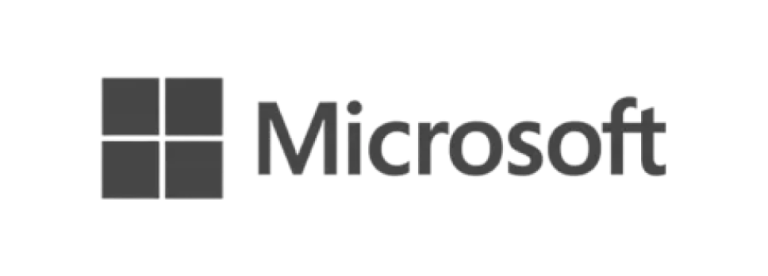
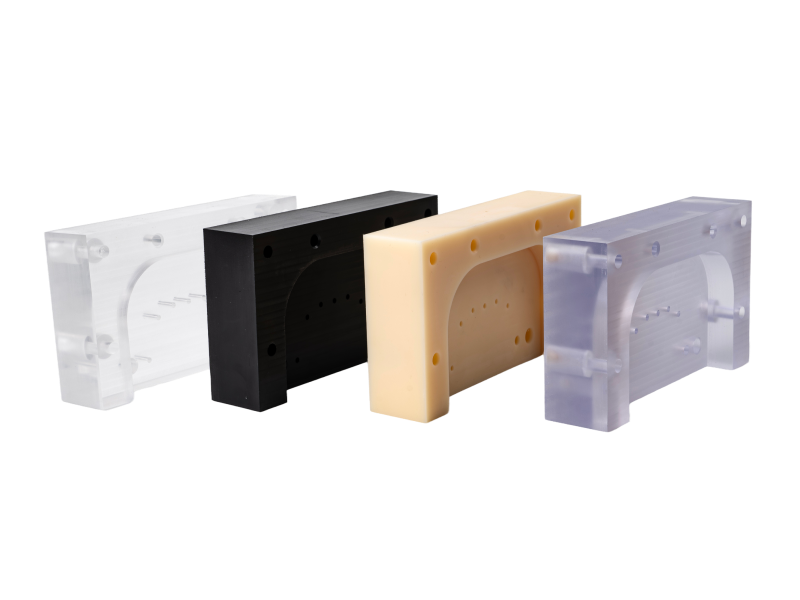
What Is Vacuum Casting?
Vacuum casting is a process that uses silicone molds to create detailed, high-quality parts. Typically, we create a master model using 3D printing or CNC machining. Once the model is ready, we use it to create silicone molds.
We then pour in a material such as polyurethane and use a vacuum to remove air bubbles and make the part smooth and precise. Vacuum casting is great for small batches, testing parts, and creating prototypes because it is affordable and can produce parts with complex geometries.
LTC is a leader in polyurethane casting services, offering domestic (China) and international economy options to fit your timeline and budget.
Our Vacuum Casting Factory
Our vacuum casting factory combines advanced techniques and skilled craftsmanship to produce precise, high-quality prototypes and low-volume parts. We deliver reliable solutions tailored to meet diverse industry needs.
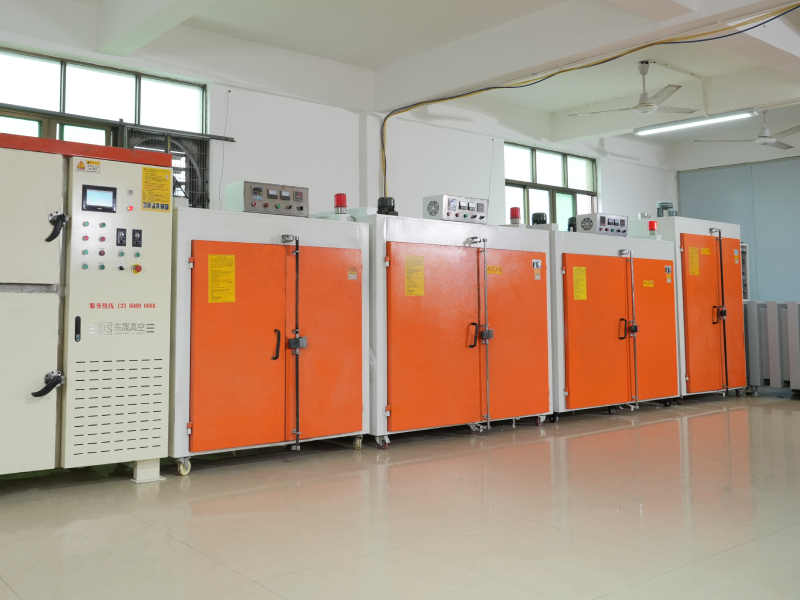
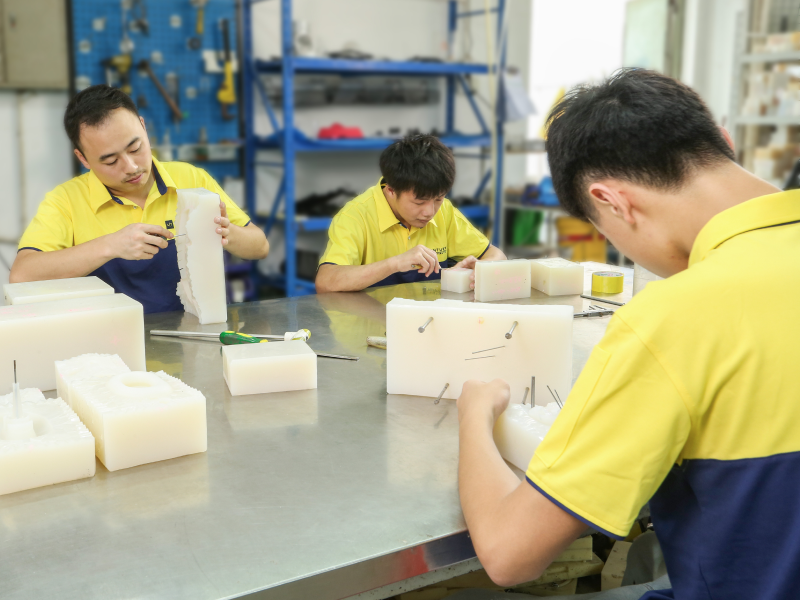
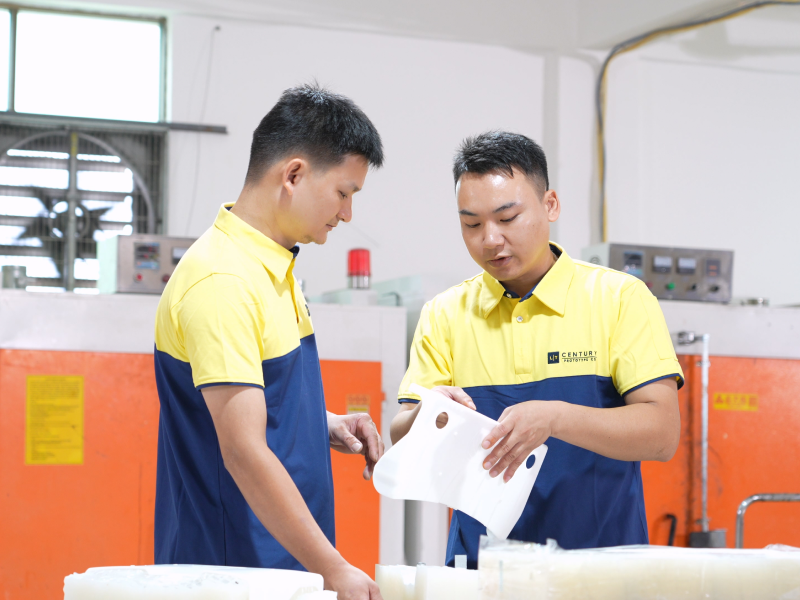
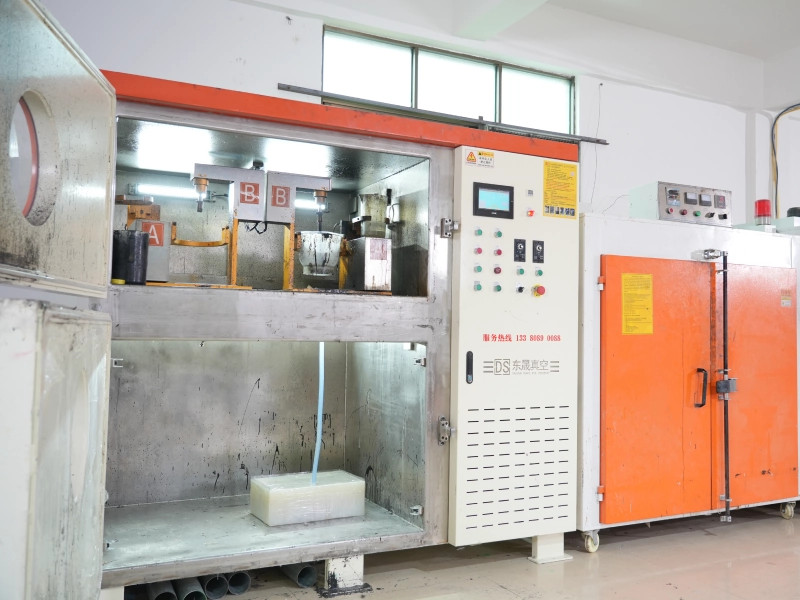
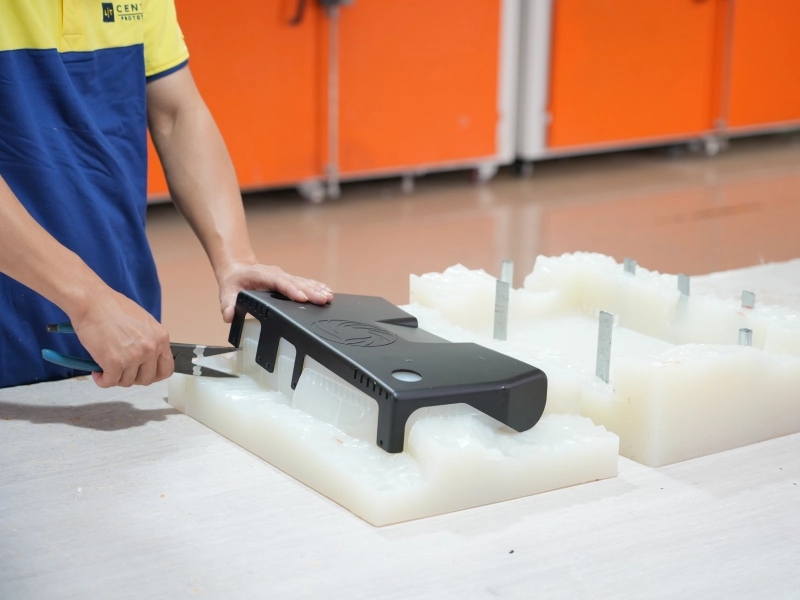
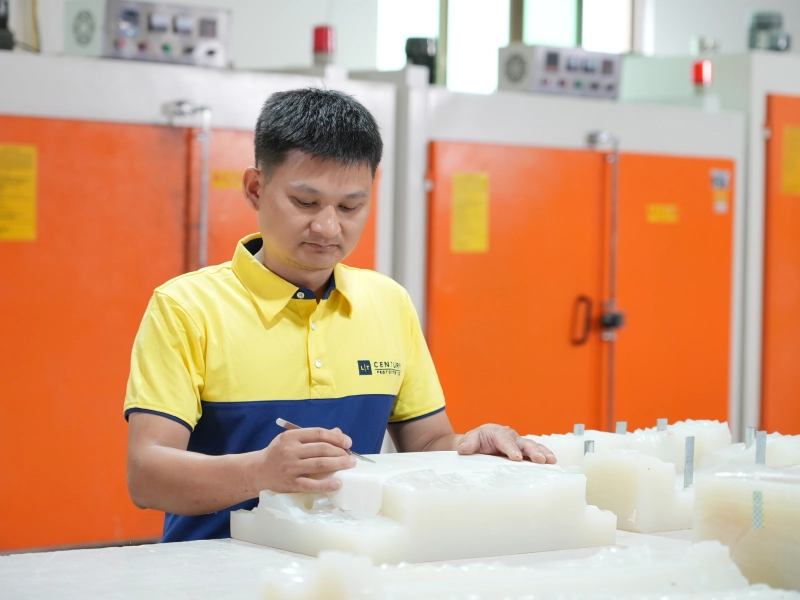
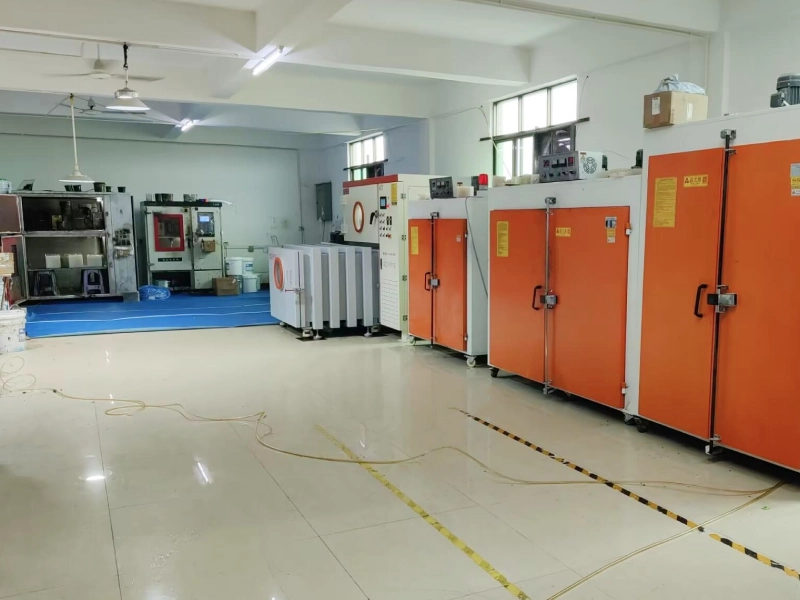
Gallery of Vacuum Casting Services Parts
Browse our gallery to see examples of high-quality parts produced through vacuum casting. From detailed prototypes to functional parts, these examples showcase the precision and versatility of our casting services.
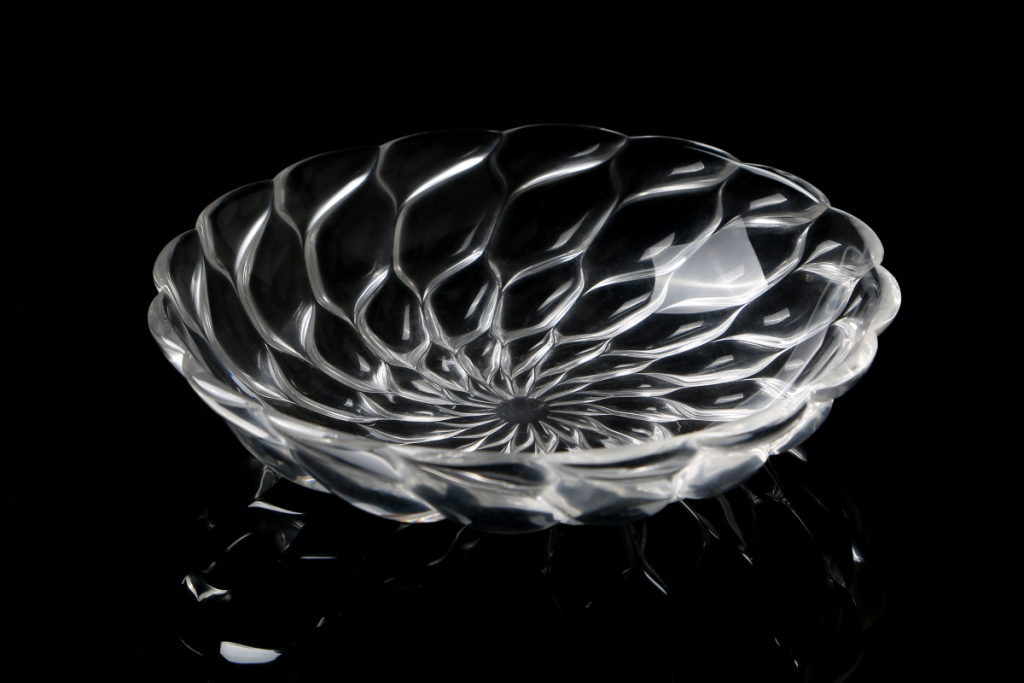
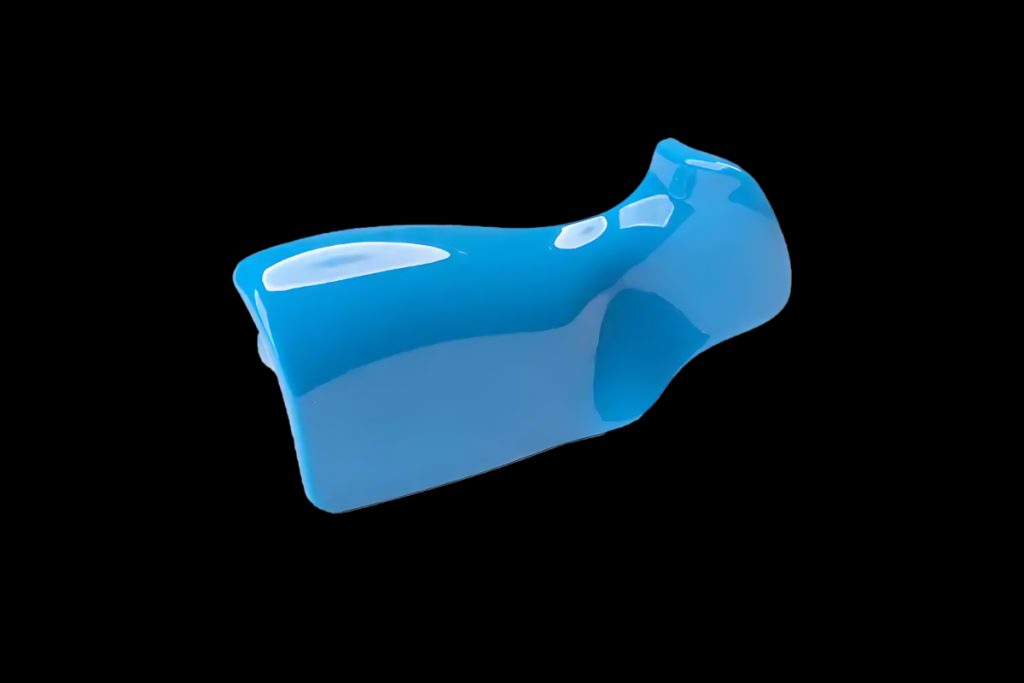
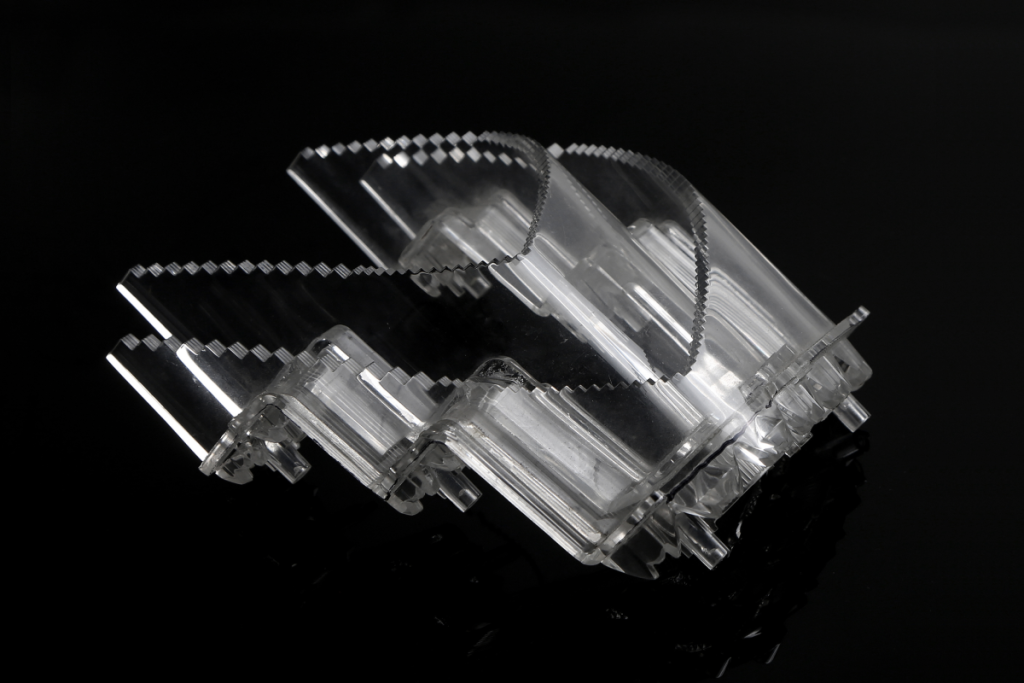
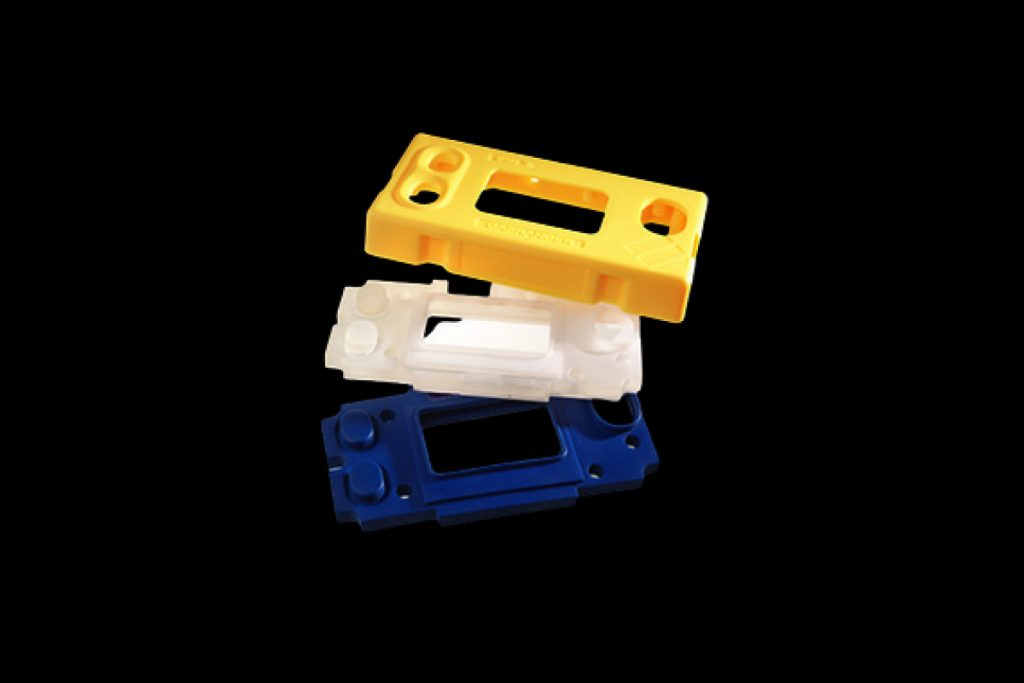
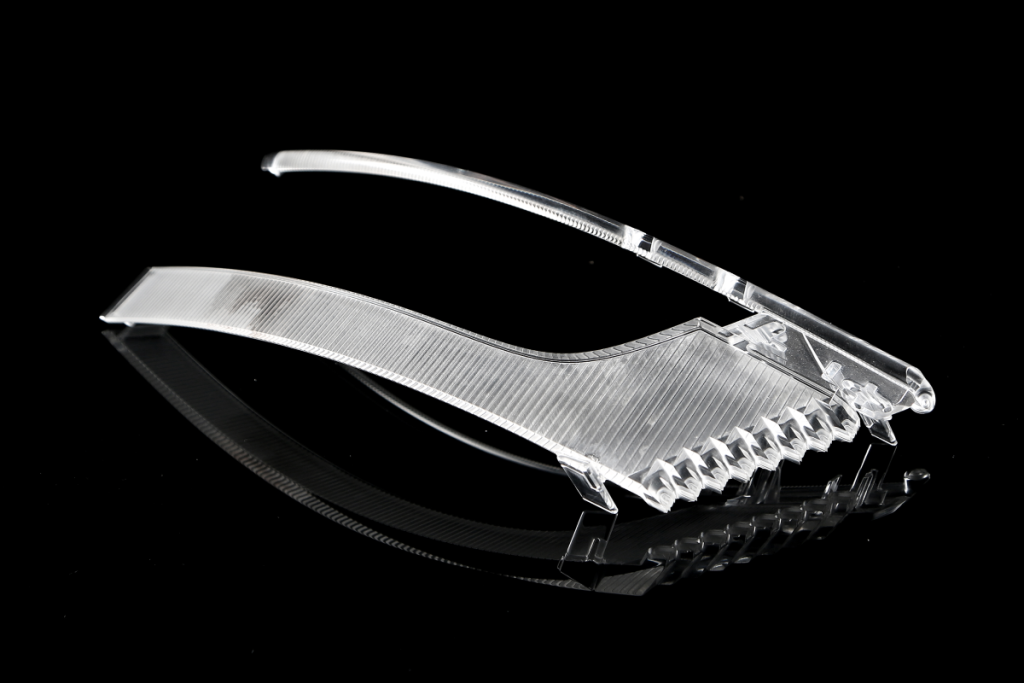
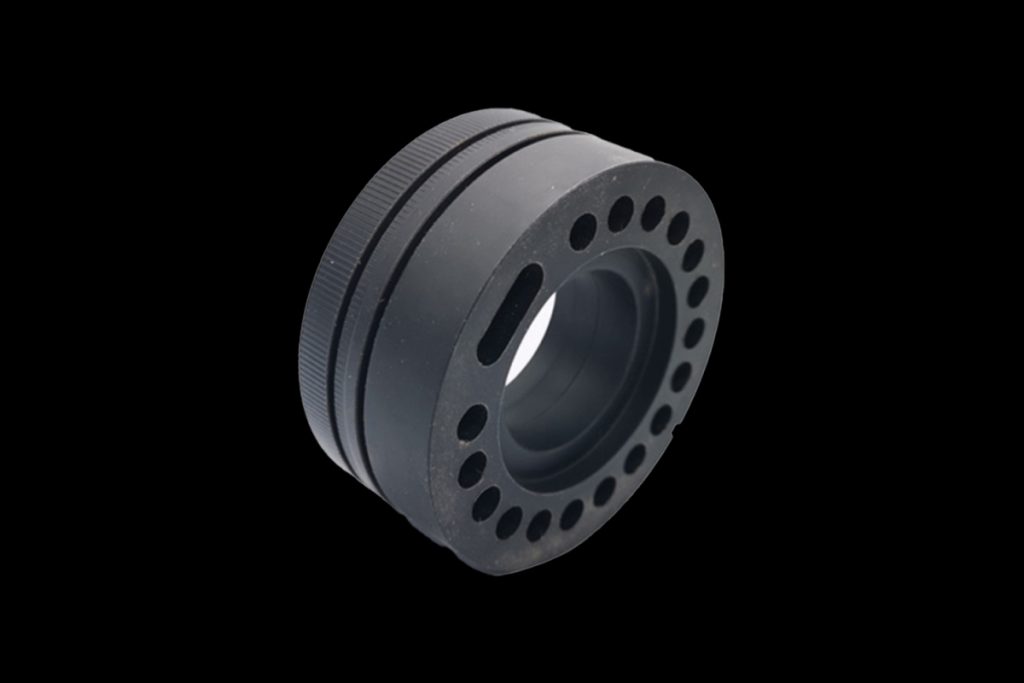
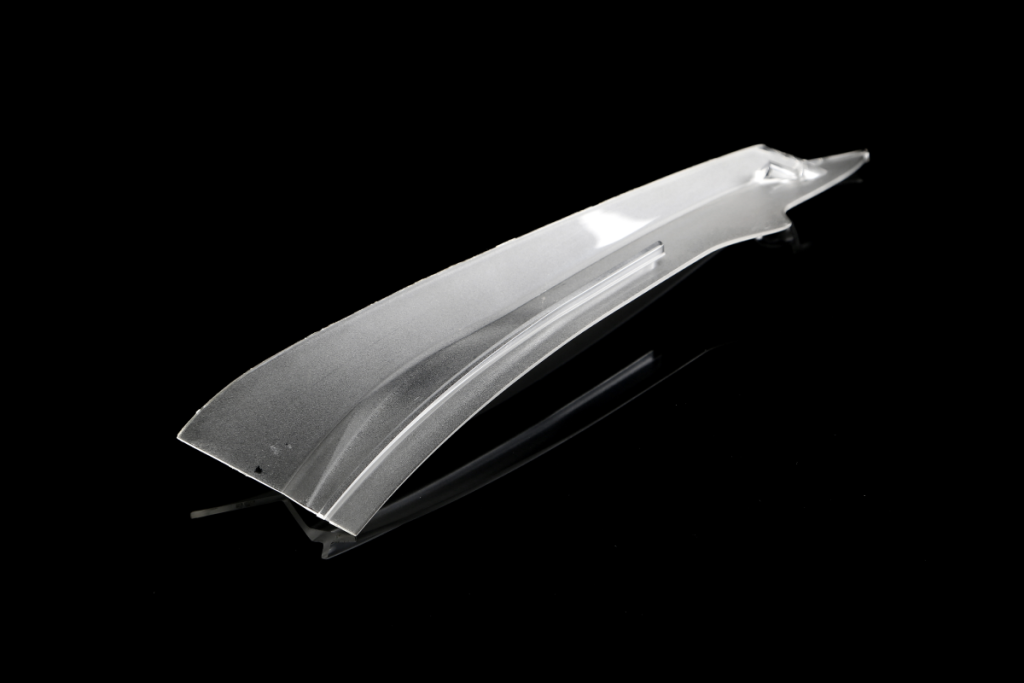
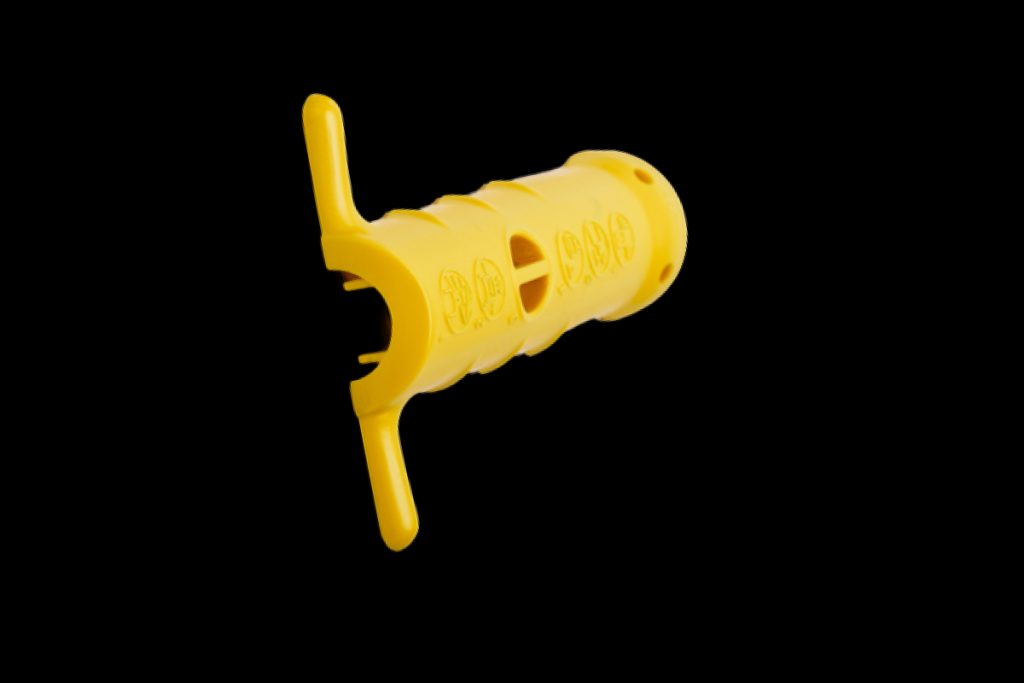
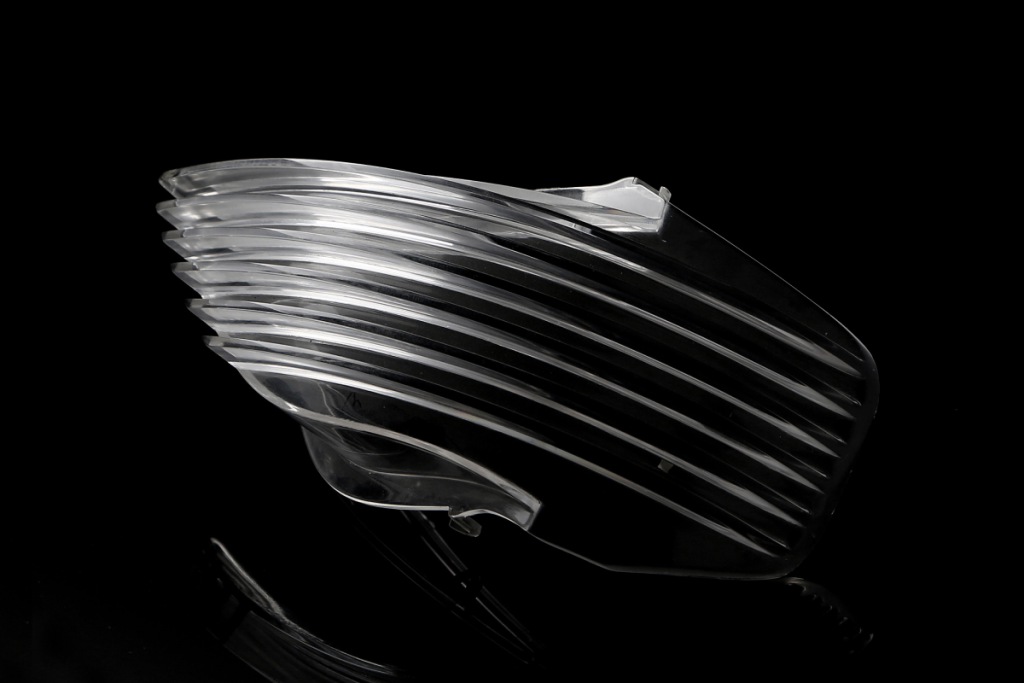
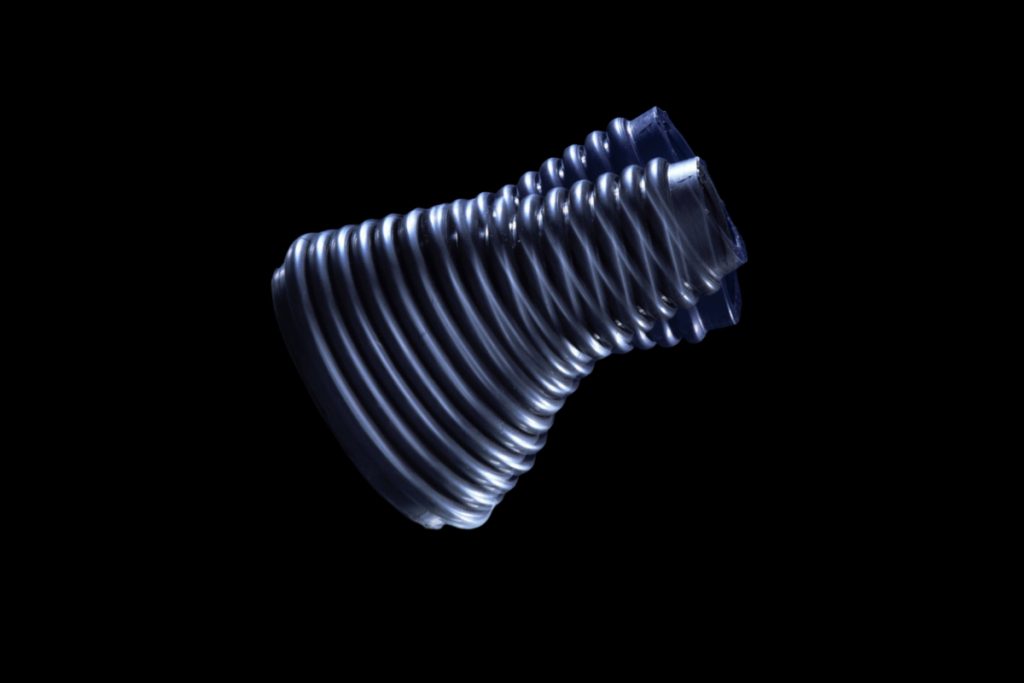
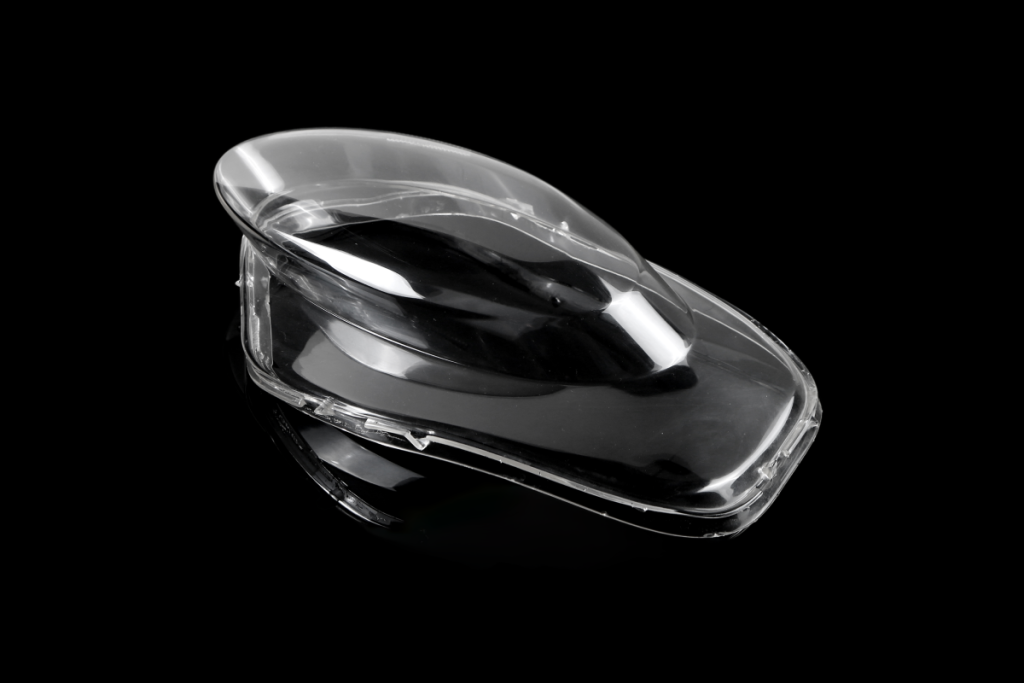
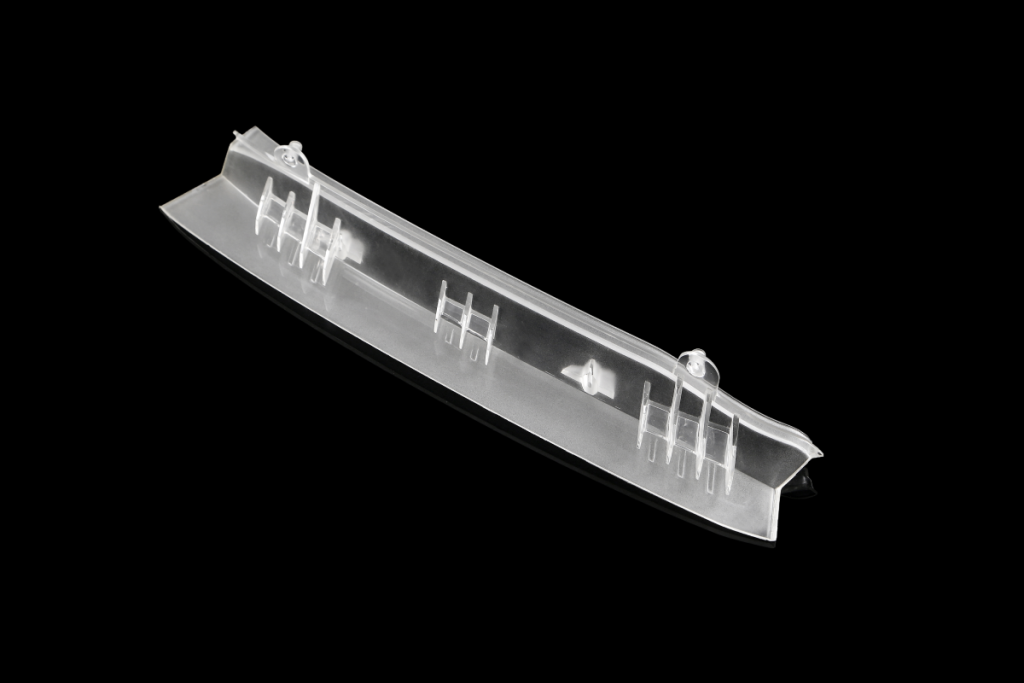
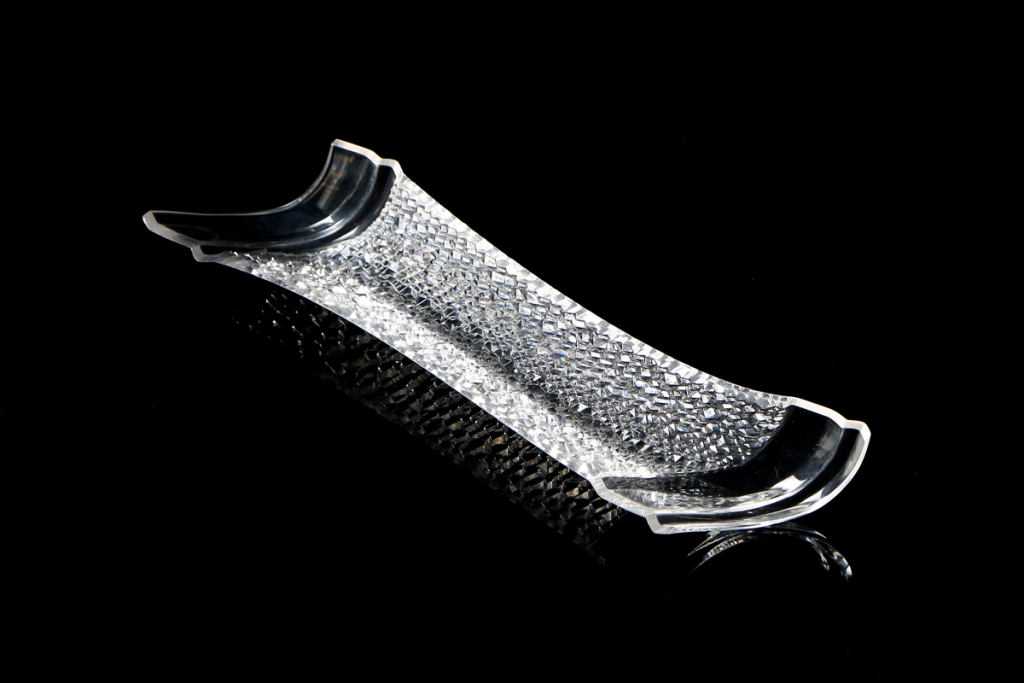
Why Choose Our Vacuum Casting Services
Skilled Manufacturer
With years of expertise, we provide custom urethane casting for automotive, electronics, and medical industries, ensuring quality craftsmanship.
Full Quality Check
We inspect every stage of vacuum casting to ensure parts meet specifications, are defect-free, and ready for use.
State-of-the-Art Equipment
Our advanced equipment ensures fast, efficient vacuum casting from prototyping to production, delivering high-quality results.
Premium Logistics Advantage
As VIP clients of DHL, UPS, and FedEx, we secure the best rates and enjoy fast, personalized service. Our skilled customs team guarantees efficient delivery, even during peak seasons, reducing the risk of delays.
Materials for Custom Vacuum Casting Service
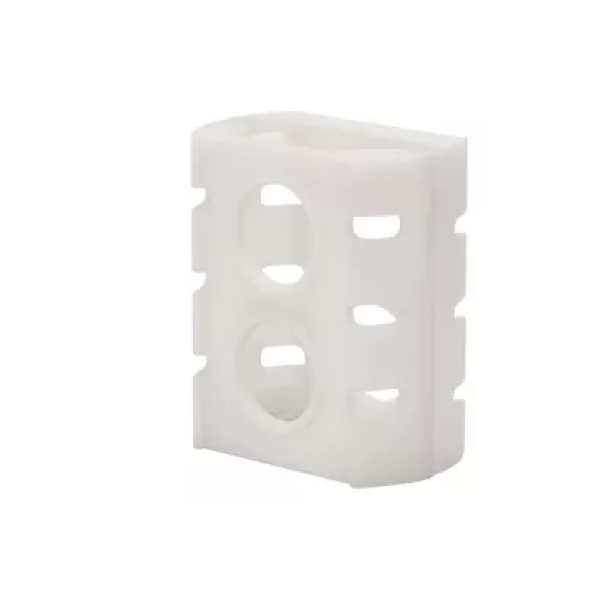
ABS-like Polyurethanes
These materials closely resemble the physical properties of ABS plastic, known for its impact resistance and toughness.
They are excellent for producing prototypes that will undergo mechanical testing, automotive components, and consumer products requiring durability and stability.
- PU8150
- PX215
- UP4280
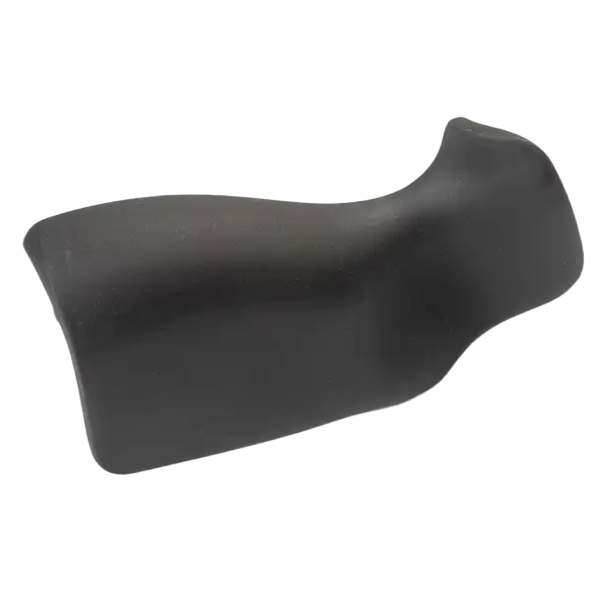
Heat-resistant ABS
Heat-resistant ABS combines the strength and impact resistance of standard ABS with enhanced thermal stability.
Ideal for applications exposed to higher temperatures, it maintains structural integrity and durability, commonly used in automotive, electrical, and industrial components.
- PX223
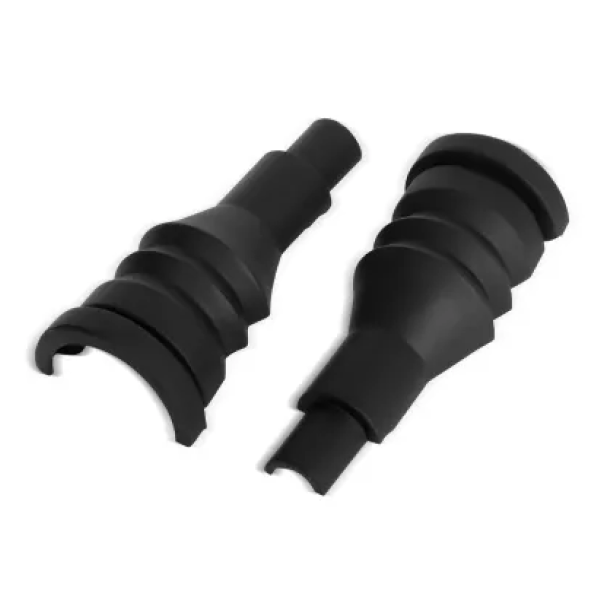
Rubber-like Polyurethanes
These materials mimic the properties of flexible rubbers and are ideal for producing parts that require elasticity, flexibility, and durability.
Applications include seals, gaskets, grips, and other components that need to withstand repetitive movement or compression.
- PU8400
- PU0387
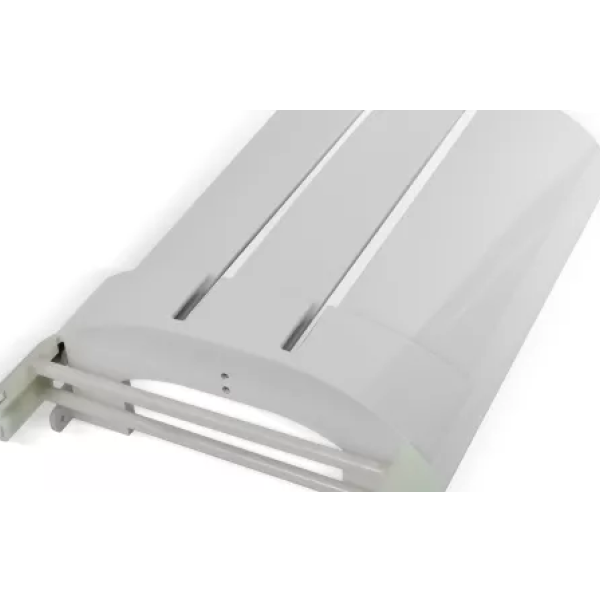
PP-like
PP-like materials are designed to replicate the properties of Polypropylene (PP), offering excellent stiffness, chemical resistance, and high heat tolerance.
They are ideal for applications requiring durability, impact resistance, and dimensional stability in various industrial and consumer products.
- UP5690
- UP8570
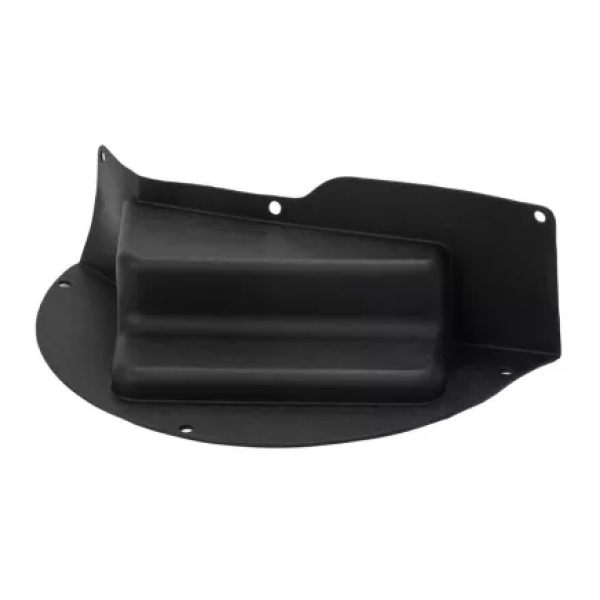
PC-like
PC/PM-like materials mimic the characteristics of Polycarbonate (PC) and Polymethyl Methacrylate (PMMA), offering high clarity, impact resistance, and UV stability.
These materials are widely used in applications requiring transparency, strength, and resistance to weathering and chemicals.
- PX521
- PX8752
Vacuum Casting Surface Finishes
Vacuum casting surface finishes include polishing, grinding, oil spraying, and electroplating, enhancing appearance, durability, and functionality of cast parts.
Name | Color | Application/Materials | Description |
---|---|---|---|
Grinding (Coating) | N/a | Vacuum Cast Parts (Resins, Plastics) | A mechanical process used to remove excess material or smooth out surfaces to achieve a uniform, rough finish on parts. |
Polishing | N/A | Vacuum Cast Parts (Resins, such as PU or other plastic-based materials) | A process to smooth the surface of parts, enhancing the gloss and reducing imperfections, providing a high-shine finish. |
Oil Spraying | N/A | Vacuum Cast Parts (Plastic/Resin Materials) | A coating process where an oil-based finish is sprayed onto the surface of parts for protection, lubrication, or aesthetic purposes. |
Electroplating | Metallic (Gold, Silver, Chrome, etc.) | Vacuum Cast Parts (Plastics, Resins, Metal-Coated Resins) | A post-processing technique where a metal coating is applied through an electrochemical process to enhance the part's durability, conductivity, and appearance. |
Manufacturing Capabilities
Check out our vacuum casting capabilities below, where we highlight production details.
Specifications | Tolerance |
---|---|
Accuracy | Achieving the highest precision with tolerances as tight as ±0.3 mm |
Maximum Part Size | Length: 1800 mm, Width: 1000 mm, Height: 600 mm |
Weight of Processed Products | Each individual item weighs less than 8 kg |
Material Thickness | 0.5 mm or above |
Mold Lifespan | Approximately 12 cycles |
The data in the figure is for reference only. For a detailed analysis, please reach out to us via email, and we’ll be happy to confirm the specifics with you.
Gallery of Vacuum Casting Services Parts
Browse our gallery to see examples of high-quality parts produced through vacuum casting. From detailed prototypes to functional parts, these examples showcase the precision and versatility of our casting services.
Vacuum Casting Tolerance
Vacuum casting tolerance ensures precise part dimensions, with minimal deviations in size and deformation for high-quality prototypes.
Part Dimensions | Tolerance Range | Deformation Tolerance |
---|---|---|
≤100 mm | ±0.3 mm | ±0.2 mm |
100-200 mm | ±0.4 mm | ±0.4 mm |
200-300 mm | ±0.5 mm | ±0.5 mm |
300-400 mm | ±0.6 mm | ±0.6 mm |
400-1000 mm | ±0.6-1.0 mm | ±1.0 mm |
The data in the figure is for reference only. For a detailed analysis, please reach out to us via email, and we’ll be happy to confirm the specifics with you.
Get Precise Vacuum Casting Parts Today!
Need high-quality, detailed parts? Contact us for fast, cost-effective vacuum casting solutions that deliver accuracy and fine details for your prototypes or low-volume production.
How to Work with Our Urethane Casting Services
Our streamlined process makes working with us simple and efficient, from initial design to finished product.
Upload CAD Design
Start by sharing your CAD design or 3D model with us through our form or email.
Quote & DFM Review
We will review your design and provide a detailed quote, along with a Design for Manufacturability (DFM) analysis to optimize your part for vacuum casting.
Order Confirmation
Once the quote is approved, we confirm your order and prepare for production, ensuring everything meets your exact specifications.
Start Production
Once your order is confirmed, production begins, and we’ll provide regular updates on the progress.
Vacuum Casting Service FAQs
Vacuum casting begins with creating a master pattern, often using a high-resolution 3D printer. This master pattern is an exact representation of the final part, capturing all the intricate details needed for the mold. Once the master pattern is ready, a silicone mold is made around it.
This process is performed under vacuum conditions to ensure that no air bubbles are trapped, which could compromise the mold’s accuracy or surface finish. After the mold cures, it is carefully opened, and the master pattern is removed, leaving a cavity shaped like the final part. The casting resin, usually a polyurethane material, is then mixed and poured into the mold.
Vacuum is applied again to eliminate any air bubbles during the pouring process, ensuring that the resin fills the mold entirely and captures all the fine details. Once the resin has cured, the part is removed from the mold. This mold can typically be reused for multiple castings, depending on the material and design. After removal, the part undergoes finishing touches, such as cleaning, sanding, or painting, to achieve the desired look and functionality.
Vacuum casting commonly uses polyurethane resins, which offer a wide range of properties similar to those found in production-grade plastics. These resins can mimic materials like ABS, polyethylene (PE), polypropylene (PP), and even rubber-like substances, making them highly versatile for various applications. The flexibility of polyurethane resins allows you to choose the most appropriate material based on the specific needs of your project.
One of the main benefits is its cost-effectiveness, particularly for producing high-quality prototypes or low-volume parts without the need for expensive tooling. The process also allows for the accurate reproduction of intricate details from the master model, providing high precision and consistency across multiple parts. Additionally, vacuum casting is ideal for creating functional prototypes that closely resemble the final product, enabling testing for form, fit, and function before moving to full-scale production. This makes it especially useful for marketing samples, pre-production models, and functional testing in various industries.
Urethane casting is often preferred for projects that require low-quantity production runs because it involves significantly lower upfront costs compared to injection molding. While injection molding is better suited for large-scale production, the high cost of creating molds can be prohibitive for smaller batches.
Urethane casting, on the other hand, allows for cost-effective production of smaller quantities, typically up to 50 parts. Thus, it is ideal for prototypes and early-stage product development. Additionally, urethane casting provides the flexibility to refine designs before committing to the more expensive and time-consuming injection molding process.
One critical consideration is maintaining consistent wall thickness. Variations in thickness can lead to uneven curing, warping, or weak spots in the finished product. A recommended range of 1.5 to 5 mm is typical, depending on the part’s size and complexity.
Another important aspect is the use of draft angles, which facilitate the easy removal of parts from the mold. Without these angles, parts may stick to the mold, leading to damage or imperfections. Undercuts and overhangs also require careful planning, as they can complicate mold design and increase production costs. In some cases, specialized molds with side-action cores or split designs may be needed to handle these features.
Additionally, incorporating ribs and gussets into the design can improve the strength and rigidity of the part without significantly increasing material usage or weight. Proper placement of vents and gates is also essential for ensuring smooth resin flow and avoiding air pockets during casting. The surface finish of the master model directly influences the appearance of the cast part, so any texture or polish applied to the master will be replicated in the final product.
Vacuum casting has some limitations, particularly with complex designs. It’s important to include draft angles for easy part removal and avoid features like deep ribs or undercuts that could damage the silicone mold during the demolding process. The silicone mold is relatively soft, so careful design is essential to ensure longevity.
Get Precision Parts with Ease – Request a Vacuum Casting Quote Today!
Need precise prototypes or small-batch parts? Contact us today to request a quote for our vacuum casting services and start your project with us.
Latest Blog
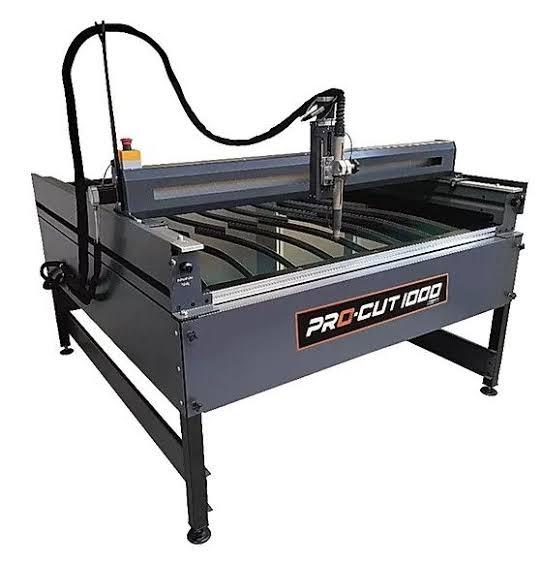
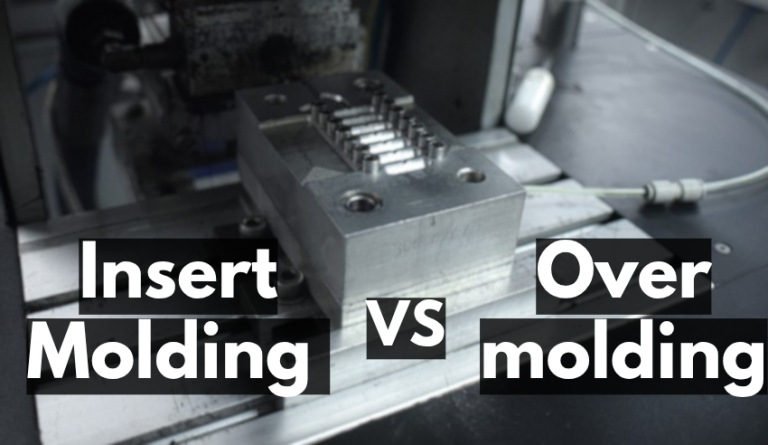